Type 7334-1 Loop Sensorfor RE01 and RE101 magnetic emission tests |
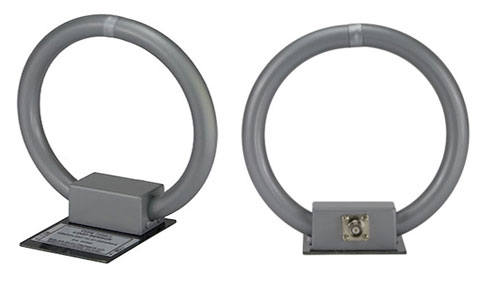
![]() |
![]() | |||||||
| |||||||
![]() |
![]() |
|
Type 7334-1 Loop Sensorfor RE01 and RE101 magnetic emission tests |
![]() |
![]() | |||||||
| |||||||
![]() |
![]() |
Product List |
item # | page links |
7334-1 | Loop Sensor, RE01, RE101 |
7429-1 | Loop Antenna, RS01 |
9229-1 | Loop Sensor, RS101 |
9230-1 | Loop Antenna, RS101 |
item # | page links |
various | 10 µF Feed-Thru Capacitors |
7525-2 | Series Capacitor, 0.1 µF, BNC |
9133-1 | 3 Phase Delta Capacitor, 10 µF |
9146-1 | 3 Phase 'Wye' capacitor, 10 µF |
item # | page links |
7415-3 | RF Coupler and High Pass Filter |
item # | page links |
various | Line Impedance Stabilization Networks EMI voltage from power lines to ground |
item # | page links |
various | RFI/EMI Current Probes and Injection Probes |
9335-2 | Multiple Impedance Coupling Clamp |
item # | page links |
various | Resistive Devices |
item # | page links |
8121-1 | Adapter for Type 7021-1 Phase Shift Network, 200 amperes |
8801-1.6 | Inductor, 1.6 mH, 10 A, VDE 0871 A1/APR 84 |
various | Calibration Fixtures |
Clock | Engineer's Clock |